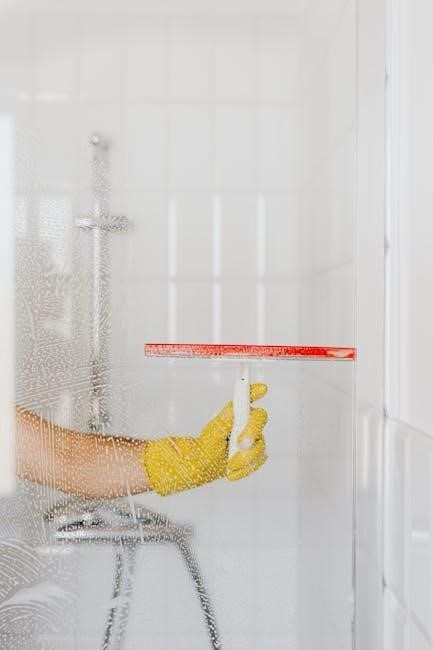
Manual Blasting: A Comprehensive Safety Guide
This guide addresses the critical aspects of manual blasting, focusing on surface preparation techniques. It will also cover identifying hazards, essential equipment, and the importance of safety protocols to protect workers in various environments.
Manual blasting, often called abrasive blasting, involves using a pressurized stream of abrasive material to clean, strip, or modify a surface. This technique is employed across diverse industries, from removing rust and paint to preparing surfaces for coatings. It is important to understand that manual blasting relies on operator control, demanding a high degree of skill and adherence to safety protocols.
The process typically involves an operator directing a nozzle connected to a blasting pot, which contains the abrasive. Compressed air propels the abrasive material towards the workpiece. Unlike automated systems, manual blasting allows for greater flexibility and precision. However, this method poses significant health and safety risks if not performed correctly. Therefore, comprehensive training and strict adherence to safety guidelines are essential for all blasting operations.
Understanding the Risks of Manual Blasting
Manual blasting presents several potential hazards that operators and employers must recognize and mitigate. One of the primary risks is exposure to hazardous dust and airborne particles generated during the blasting process. These particles can contain toxic substances, such as silica, lead, or other heavy metals, depending on the abrasive material and the surface being blasted. Inhalation of these particles can lead to serious respiratory illnesses, including silicosis, lung cancer, and other chronic conditions.
Additionally, the high-pressure stream of abrasive material can cause severe injuries, such as lacerations, abrasions, and eye damage. The noise levels produced during blasting operations can also pose a risk to hearing. Furthermore, the physical demands of manual blasting, including prolonged standing, repetitive motions, and awkward postures, can contribute to musculoskeletal disorders. Proper risk assessment, engineering controls, and the use of personal protective equipment (PPE) are crucial for minimizing these risks.
Essential Personal Protective Equipment (PPE)
Selecting and using appropriate personal protective equipment (PPE) is paramount in mitigating the hazards associated with manual blasting. Comprehensive PPE ensembles are essential for safeguarding operators from respiratory risks, eye injuries, hearing damage, and physical harm. Respiratory protection, such as air-supplied respirators, is critical for preventing the inhalation of hazardous dust and fumes. Eye and face protection, including safety glasses or face shields, is necessary to shield against flying debris and abrasive particles.
Hearing protection, such as earplugs or earmuffs, is essential for minimizing exposure to high noise levels. Body protection, including heavy-duty gloves, aprons, and protective clothing, is necessary to prevent skin abrasions and lacerations. Furthermore, the PPE must be properly fitted, maintained, and regularly inspected to ensure its effectiveness. Training on the correct use, care, and limitations of PPE is also essential. Consistent adherence to PPE protocols is a cornerstone of manual blasting safety.
Respiratory Protection
Effective respiratory protection is non-negotiable in manual blasting operations due to the high risk of inhaling hazardous airborne particles. The selection of respiratory equipment must be based on a comprehensive assessment of the contaminants present and their concentrations. Air-supplied respirators, which provide a continuous flow of clean air from an external source, are often the most suitable choice for abrasive blasting to ensure the worker’s safety.
These respirators prevent the inhalation of dust, fumes, and other harmful substances generated during the blasting process. Proper fit testing is essential to guarantee a tight seal between the respirator and the operator’s face, preventing contaminant leakage. Regular inspection, maintenance, and cleaning of respirators are also crucial to ensure their continued effectiveness. Training on the correct donning, doffing, and use of respirators is vital for all operators. A well-maintained and properly used respirator is a worker’s first line of defense against respiratory hazards in manual blasting.
Hearing Protection
Manual blasting operations often generate high noise levels, posing a significant risk to workers’ hearing. Prolonged exposure to these elevated sound levels can lead to irreversible hearing damage, including hearing loss and tinnitus. Therefore, providing adequate hearing protection is a critical safety measure in blasting environments.
Hearing protection devices, such as earplugs and earmuffs, should be readily available and mandatory for all personnel within the vicinity of the blasting operation. The choice between earplugs and earmuffs depends on individual preferences and the level of noise attenuation required. Proper fitting of hearing protection is essential to ensure its effectiveness. Workers should receive training on the correct insertion and maintenance of earplugs, as well as the proper adjustment and care of earmuffs. Regular monitoring of noise levels and consistent enforcement of hearing protection policies are crucial for safeguarding workers’ auditory health in manual blasting.
Eye and Face Protection
Manual blasting propels abrasive materials at high speeds, creating a hazardous environment for the eyes and face. Flying debris, ricocheting particles, and dust pose a significant risk of eye injuries, including corneal abrasions, punctures, and even blindness. Face shields and safety glasses are essential components of personal protective equipment (PPE) for blasters, providing a crucial barrier against these hazards.
Safety glasses should meet ANSI standards, offering impact resistance and side protection. Face shields should cover the entire face, protecting against splashes and larger debris. It is imperative to ensure that the chosen eye and face protection is appropriate for the specific blasting operation and that it fits comfortably and securely. Regular inspection and maintenance of eye and face protection are essential to ensure its effectiveness. Damaged or worn-out equipment should be replaced immediately. Workers must receive training on the proper use, care, and limitations of eye and face protection to minimize the risk of injuries during manual blasting.
Body Protection
Protecting the body during manual blasting is critical due to the potential for abrasive materials to cause skin abrasions, impacts, and embedded particles. Appropriate body protection minimizes these risks and ensures worker safety. Coveralls made of durable materials, such as heavy-duty canvas or leather, are recommended to shield the skin from direct exposure. These coveralls should be designed to resist penetration by abrasive particles and offer sufficient coverage of the torso, arms, and legs.
Aprons, particularly those made of leather or rubber, can provide an additional layer of protection for the front of the body, especially during operations where there is a high risk of ricocheting particles. Gloves are essential for hand protection, preventing abrasions and impacts. Footwear should also be durable and offer adequate protection against falling objects and sharp debris. Proper fit and maintenance of body protection are crucial. Regularly inspect coveralls, aprons, gloves, and footwear for wear and tear, replacing damaged items promptly. Workers should be trained on the correct usage and care of body protection to ensure maximum effectiveness during manual blasting activities.
Safe Blasting Techniques and Procedures
Implementing safe blasting techniques and procedures is crucial for minimizing risks and ensuring the well-being of operators. Before commencing any blasting operation, conduct a thorough risk assessment to identify potential hazards and implement appropriate control measures. Ensure that all workers involved are adequately trained and competent in the safe operation of blasting equipment and procedures. Establish clear communication protocols to coordinate activities and prevent accidents.
Maintain a safe distance from the blasting area and use barriers or signage to restrict access to unauthorized personnel. When blasting, always direct the nozzle away from yourself and others, and avoid blasting in windy conditions to prevent the spread of hazardous materials. Regularly inspect equipment for defects and ensure it is in good working order before use. Use proper ventilation to minimize exposure to dust and fumes, and wear appropriate personal protective equipment (PPE), including respiratory protection, eye and face protection, hearing protection, and body protection.
Adhere to established safety guidelines and regulations, and report any incidents or near misses promptly.
Equipment Inspection and Maintenance
Regular equipment inspection and maintenance are paramount for ensuring the safe and efficient operation of blasting equipment. Establish a routine inspection schedule to identify potential issues before they escalate into hazards. Inspect hoses, nozzles, and connections for wear, damage, or leaks, and replace them as needed.
Check the abrasive blasting pot for structural integrity and ensure that all safety devices, such as pressure relief valves, are functioning correctly. Inspect the air compressor for proper operation and ensure that it is delivering clean, dry air at the correct pressure. Verify that the ventilation system is working effectively and that filters are clean and unobstructed. Regularly clean and maintain all blasting equipment to prevent the buildup of dust and debris, which can impair performance and create safety hazards.
Keep a detailed record of all inspections and maintenance activities, and promptly address any identified issues. Only qualified personnel should perform repairs and maintenance on blasting equipment. By prioritizing equipment inspection and maintenance, you can minimize the risk of accidents, extend the lifespan of your equipment, and maintain a safe working environment.
Workplace Ventilation and Air Quality
Maintaining adequate workplace ventilation and air quality is critical in manual blasting operations to protect workers from hazardous dust and fumes. Implement a comprehensive ventilation system that effectively removes airborne contaminants from the blasting area. Use local exhaust ventilation (LEV) systems, such as dust collectors or fume extractors, to capture contaminants at their source.
Ensure that the ventilation system is properly designed, installed, and maintained, and that it meets all relevant regulatory requirements. Regularly inspect and clean ventilation filters to maintain optimal performance. Monitor air quality in the blasting area to ensure that contaminant levels are within permissible exposure limits (PELs). Conduct air sampling to identify and quantify airborne hazards, such as silica dust, metal fumes, or organic vapors.
Provide workers with appropriate respiratory protection, such as respirators or supplied-air hoods, when engineering controls are not sufficient to maintain safe air quality. Train workers on the proper use, maintenance, and limitations of respiratory protection. By prioritizing workplace ventilation and air quality, you can create a healthier and safer working environment, reduce the risk of respiratory illnesses, and comply with regulatory standards.
Emergency Procedures and First Aid
Establish clear emergency procedures and first aid protocols for manual blasting operations to ensure a swift and effective response to accidents or injuries. Develop a comprehensive emergency action plan that outlines specific procedures for various scenarios, such as respiratory distress, eye injuries, lacerations, or exposure to hazardous materials. Ensure that all workers are thoroughly trained on the emergency action plan and their respective roles.
Maintain a well-stocked first aid kit in a readily accessible location, equipped with essential supplies for treating common blasting-related injuries. Designate trained first responders who are certified in CPR, first aid, and the use of automated external defibrillators (AEDs). Conduct regular drills and simulations to practice emergency procedures and identify areas for improvement.
Establish clear communication channels to report emergencies and alert emergency services, such as local fire departments or medical facilities. Keep emergency contact information readily available. In the event of an injury or exposure, provide immediate first aid and seek professional medical attention as needed. Document all incidents and injuries to identify trends and implement corrective actions to prevent future occurrences. Prioritizing emergency procedures and first aid preparedness is essential to protect workers’ health and safety and minimize the impact of accidents.
Training and Education for Blasters
Comprehensive training and education are paramount for ensuring the competence and safety of blasters involved in manual blasting operations. Develop a structured training program that covers all aspects of blasting, including equipment operation, hazard identification, risk assessment, and safety protocols. Provide hands-on training that allows blasters to practice blasting techniques under the supervision of experienced instructors.
Ensure that training programs comply with relevant regulatory requirements and industry standards. Emphasize the importance of personal protective equipment (PPE) and proper usage. Educate blasters on the health hazards associated with exposure to dust, fumes, and noise during blasting operations. Provide ongoing education to keep blasters up-to-date on the latest blasting techniques, safety procedures, and regulatory changes.
Encourage blasters to participate in refresher courses and professional development opportunities to enhance their skills and knowledge. Conduct regular assessments and evaluations to ensure that blasters maintain their competency. Foster a culture of continuous learning and improvement. By investing in thorough training and education, employers can empower blasters to perform their jobs safely and effectively, reducing the risk of accidents and injuries. Document all training sessions.
Environmental Considerations and Waste Disposal
Environmental responsibility is vital in manual blasting. Implement practices to minimize environmental impact and ensure proper waste disposal. Identify and assess potential environmental hazards associated with blasting, including dust emissions, noise pollution, and abrasive waste. Select abrasive materials that are environmentally friendly and non-toxic.
Implement dust control measures, such as using wet blasting techniques or enclosing blasting areas, to minimize airborne particulate matter. Monitor noise levels and implement noise reduction strategies. Develop a comprehensive waste disposal plan for abrasive materials, spent filters, and other blasting-related waste. Segregate hazardous waste from non-hazardous waste. Dispose of hazardous waste in accordance with local, state, and federal regulations.
Recycle abrasive materials whenever possible to reduce waste and conserve resources. Ensure that all waste disposal activities are properly documented. Regularly inspect blasting equipment and facilities to identify and address potential environmental concerns. Provide training to blasters on environmental best practices and waste disposal procedures. By prioritizing environmental stewardship and responsible waste disposal, organizations can minimize their impact on the planet and promote a sustainable future for blasting operations.
Regulatory Compliance and Standards
Adhering to regulatory compliance and industry standards is crucial for ensuring the safety and legality of manual blasting operations. Familiarize yourself with all applicable federal, state, and local regulations pertaining to abrasive blasting.
These regulations may cover aspects such as worker safety, environmental protection, and waste disposal. Stay up-to-date on any changes or updates to these regulations. Comply with Occupational Safety and Health Administration (OSHA) standards related to abrasive blasting, including requirements for personal protective equipment (PPE), ventilation, and respiratory protection.
Adhere to environmental regulations set forth by the Environmental Protection Agency (EPA), such as those pertaining to air emissions and hazardous waste management. Obtain any necessary permits or licenses required for blasting operations in your jurisdiction. Implement a system for tracking and documenting compliance with all applicable regulations and standards. Regularly audit blasting operations to identify and address any compliance gaps. Provide training to blasters on regulatory requirements and industry best practices. By prioritizing regulatory compliance and adhering to industry standards, organizations can protect their workers, the environment, and their bottom line.
Additional Safety Tips for Blasting Operations
Beyond the core safety procedures, several additional tips can enhance the overall safety of blasting operations. Implement a buddy system, ensuring that blasters work in pairs to provide mutual assistance and monitor each other’s well-being. Conduct regular toolbox talks to reinforce safety procedures, discuss recent incidents, and address any concerns raised by workers.
Maintain clear communication channels between blasters, supervisors, and other personnel involved in the operation. Establish a system for reporting hazards, near misses, and incidents promptly and effectively. Encourage workers to actively participate in safety discussions and contribute to the development of safety improvements.
Provide adequate lighting in the blasting area to ensure good visibility and reduce the risk of accidents. Keep the work area clean and free from obstructions to prevent trips, falls, and other hazards. Regularly inspect and maintain all blasting equipment, including hoses, nozzles, and pressure gauges. Ensure that all workers are properly trained in the safe use of blasting equipment. By implementing these additional safety tips, organizations can create a safer and more productive blasting environment for their workers.